نقش عناصر آلیاژی در ورق استیل
- بازدید:1569
- کامنت:0
- یک شنبه, 14 شهریور 1400
نقش عناصر آلیاژی در ورق استیل
ورق استیل حاوی عناصر آلیاژی متعددی است که همسو و مرتبط با گرید و ترکیبات شیمیایی خاص می باشد. در بخش های ذیل افزودنیهای آلیاژی و دلایل حضور این افزودنی ها در آلیاژ و جدول خلاصه ای شامل همه عناصر آلیاژی توضیح داده می شود.
کربن
کربن و آهن باهم ترکیب می شوند تا فولاد به وجود آید. این عمل باعث تقویت استحکام و سختی آهن می شود. عملیات حرارتی برای تقویت و استحکام بخشیدن و سخت کردن آهن خالص کافی نیست اما وقتی کربن به آن اضافه می شود محدوده وسیعی از استحکام و سختی در آن مشاهده می گردد.
در ورق استیل فریتی و آستنیتی میزان کربن زیاد علی الخصوص برای اهداف جوشکاری به لحاظ خطر رسوب کاربید، ترجیح داده نمیشود.
منگنز
افزودن منگنز به فولاد سبب ارتقاء خواص گرم کاری و تقویت چقرمگی، استحکام و سختی پذیری در آن میشود. منگنز دقیقاً مثل نیکل، عنصری است جهت تشکیل آستنیت و به طور سنتی به عنوان جایگزینی برای نیکل در استیل های سری 200 برای ورق استیل های آستنیتی بکار می رفته است، کما اینکه ورق استیل ۲۰۲ جایگزین ورق استیل ۳۰۴ می باشد.
کروم
کروم به منظور ارتقاء مقاومت در برابر اکسیداسیون اضافه می گردد. چنانچه کروم بیشتری افزوده شود، این مقاومت هم بیشتر می شود.
ورق استیل حداقل 10.5 درصد کروم دارد که معمولاً ۱۱ تا ۱۲ درصد می باشد و سطح قابل توجهی از مقاومت خوردگی را در مقایسه با استیل های با درصد کروم پایین تر نشان می دهد.
مقاومت خوردگی به پدیده تشکیل یک لایه اکسید کروم بی اثر و خود ترمیم گر روی سطح ورق استیل منتسب می باشد.
نیکل
برای تولید مهمترین گروه استیل هایی که هم مقاوم به حرارت باشند و هم مقاومت به خوردگی، مقادیر زیاد نیکل -بیش از 8 درصد- به استنلس استیل کروم بالا اضافه می گردد. این گروه شامل ورق استیل های آستنیتی است که با 18-8 یا 1.4301 مشخص می شوند. در این گروه، نیکل است که با تشکیل آستنیت کمک میکند به استحکام زیاد و چقرمگی عالی یا استحکام ضربه های، هم در دماهای زیاد و هم کم. نیکل همچنین مقاومت خوردگی و مقاومت در برابر اکسیداسیون را به طور قابل ملاحظه ای افزایش می دهد.
مولیبدن
مولیبدن هنگامی که با استیل های آستنیتی کروم-نیکل دار ترکیب یا آلیاژ شود، باعث تقویت و ازدیاد مقاومت در برابر خوردگی شیاری و خوردگی حفرهای به ویژه در محیط های حاوی گوگرد و کلرید می شود.
نیتروژن
نیتروژن همانند نیکل، عنصری است که باعث تشکیل آستنیت شده و ثبات آن را در استنلس استیل ها بالا می برد. زمانی که نیتروژن با ورق استیل ترکیب شود، استحکام تسلیم همراه با مقاومت خوردگی حفره ای افزایش یافته، به طور چشمگیری تقویت میگردد.
مس
در حوزه ورق استیل، مس اغلب عنوان عنصری رسوبی یا پس مانده معرفی می شود. این عنصر به آلیاژ های متعددی افزوده می شود تا خواص و ویژگی های رسوب سختی را ایجاد نماید یا مقاومت خوردگی را بالا ببرد، عمدتاً در شرایط و محیط های آلوده به اسید سولفوریک و آب دریا.
تیتانیوم
تیتانیوم اغلب جهت تثبیت کاربید اضافه می شود خصوصاً زمانی که متریال می بایست جوشکاری شود. تیتانیوم با کربن ترکیب و باعث تشکیل کاربید تیتانیوم میشود که ترکیبی از نسبتاً پایدار و با ثبات و به راحتی در استیل نمیتواند حل شود، که همین موضوع احتمالاً موجب کاهش خوردگی بین دانه ای می گردد. هنگامی که حدوداً 0.25 تا 0.60 درصد تیتانیوم افزوده گردد، موجب میشود کربن با تیتانیوم ترکیب شود، در عین حالیکه با کروم مغایر و مخالفت مخالف می باشد و مانع از ترکیب کروم مقاوم به خوردگی، تحت عنوان کاربید های بین دانه ای و مرتبط با از دست رفتن مقاومت خوردگی در مرزهای دانه می شود.
طی چندین سال گذشته کاربرد تیتانیوم به لحاظ توانایی استیل سازان در عرضه استیل های با محتوای کربن فوق العاده پایین، به طور چشمگیری کاهش یافته است. این گونه فولاد، بدون هیچگونه نیاز به پایدارسازی یا تثبیت، به راحتی جوشکاری می شوند.
فسفر
به منظور افزایش قابلیت ماشینکاری، اغلب فسفر به گوگرد افزوده می شود، در حالی که وجود فسفر در ورق استیل آستنیتی سبب تقویت استحکام می گردد. از طرف دیگر اثری مخرب بر مقاومت خوردگی دارد و آن اینکه میل به شکست متریال در طول جوشکاری را افزایش می دهد.
گوگرد
گوگل زمانی که در مقادیر جزئی افزوده گردد سبب بهبود و ارتقاء قابلیت ماشین کاری می شود، لیکن درست مثل فسفر، اثر منفی بر مقاومت خوردگی و جوش پذیری دارد.
سلنیوم
سلنیوم در گذشته به عنوان یک افزودنی جهت تقویت ماشین کاری به کار می رفت.
نئوبیوم/ کلمبیوم
با افزودن نئوبیوم به فولاد، تثبیت کربن حاصل می شود و مانند تیتانیوم، به همان شکل عمل میکند. مضافاً اینکه نئوبیوم، آلیاژها و فولادها را برای کار در شرایط دمای بالا، قوی و محکم می سازد.
سیلیسیوم
سیلیسیوم معمولاً به عنوان عامل از بین برنده اکسیداسیون در فرآیند ذوب فولاد مورد استفاده است. مقدار ناچیزی سیلیسیم در اغلب فولادها به کار می رود.
کبالت
کبالت هنگامی که در راکتورهای هستهای در معرض تشعشع قوی قرار میگیرد، شدیداً رادیواکتیو میشود. از این رو تمامی ورق استیل های مستقر در تأسیسات هستهای از نظر وجود کبالت محدودیت مسلم و معینی خواهند داشت که اغلب حداکثر 0.2 درصد است.
این موضوع مهمی است، زیرا مقدار کبالت باقیمانده، در نیکل حضور خواهد داشت، در نیکلی که جهت تولید و ساخت ورق استیل های آستنیتی مورد استفاده است.
کلسیم
کلسیم با هدف تقویت قابلیت ماشینکاری، در مقادیر جزئی اضافه می گردد بدون اینکه هیچگونه اثر مخربی بر دیگر خواص فولاد -نظیر آنچه که سلنیوم، فسفر و گوگرد انجام میدهند- داشته باشد.
جدول ذیل تاثیرات عناصر آلیاژی را بر ویژگی ها و خواص استنلس استیل نشان میدهد
جدول اثرات عناصر آلیاژی بر خواص ورق استیل
Ti or Nb | Se | Mo | Cu | P | Si | Mn | S | Ni | Cr | C | خواص |
- | - | √ | - | √ | - | - | X | √ | √ | - | مقاومت خوردگی |
√ | - | √ | √ | √ | √ | √ | - | - | √ | √ | خواص مکانیکی |
√ | - | √ | - | - | - | - | X | √ | √ | - | مقاومت دوا بالا |
- | √ | - | - | √ | - | - | √ | - | X | X | قابلیت ماشینکاری |
√ | - | √ | - | X | - | √ | X | - | X | X | جوش پذیری |
- | - | - | √ | - | - | - | X | √ | X | X | قابلیت کار سرد |
√ = سودمند
X = مخرب
آخرین مطالب
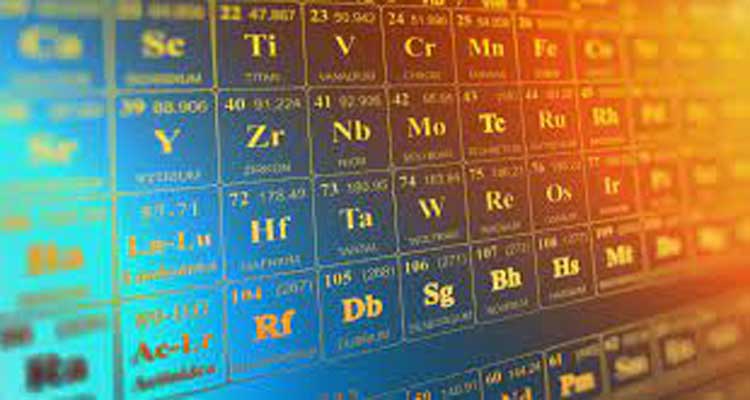
اسپانیا تولید فولاد را در ماه نوامبر 4.2 درصد ماه به ماه کاهش داد
یک شنبه, 14 شهریور 1400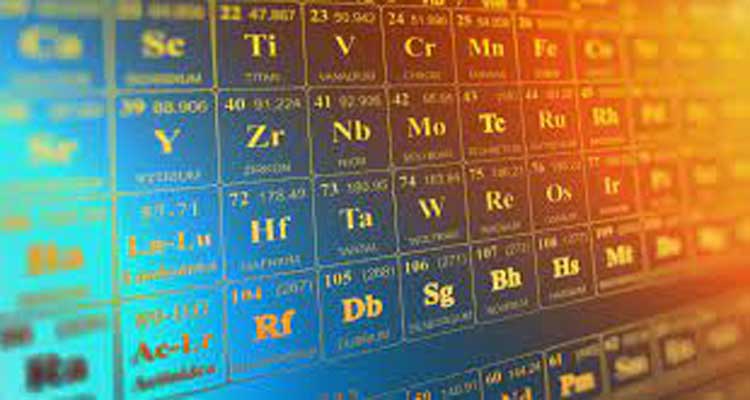
استرالیا تثبیت قیمت زغال سنگ کک را پیش بینی می کند
یک شنبه, 14 شهریور 1400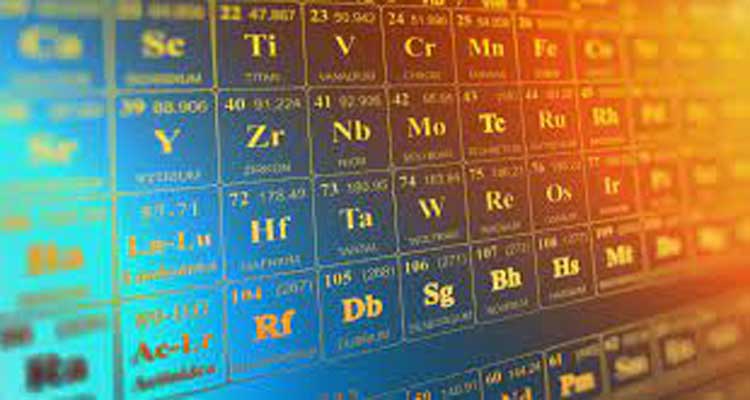
فولاد ضد زنگ هایپر دوبلکس
یک شنبه, 14 شهریور 1400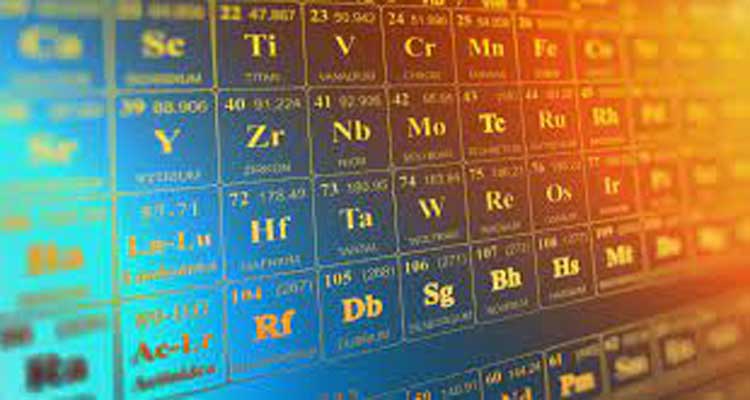
تقاضای فولاد در چین در سال 2025 به میزان 1.5 درصد سال به سال کاهش می یابد
یک شنبه, 14 شهریور 1400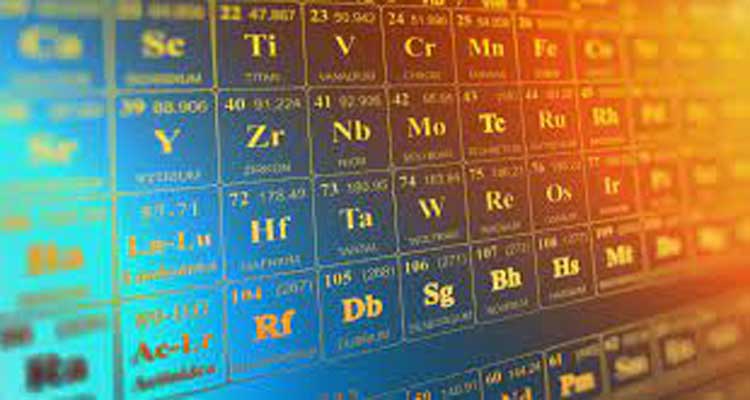
صادرات فولاد چین در سال 2024 از رکورد سال 2015 فراتر می رود
یک شنبه, 14 شهریور 1400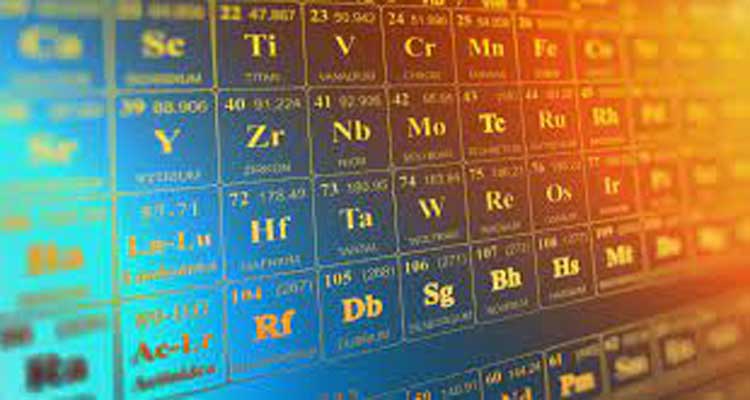
بانک مرکزی فرانسه پیش بینی رشد اقتصادی خود برای سال 2025 را کاهش داد
یک شنبه, 14 شهریور 1400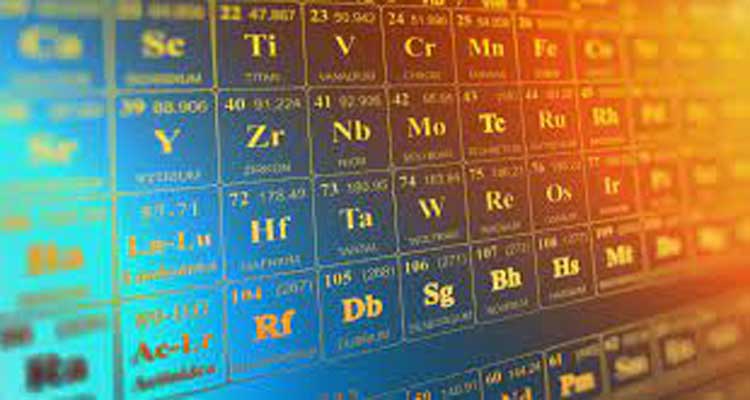
قیمت سنگ آهن در سال 2025 تحت فشار باقی می ماند
یک شنبه, 14 شهریور 1400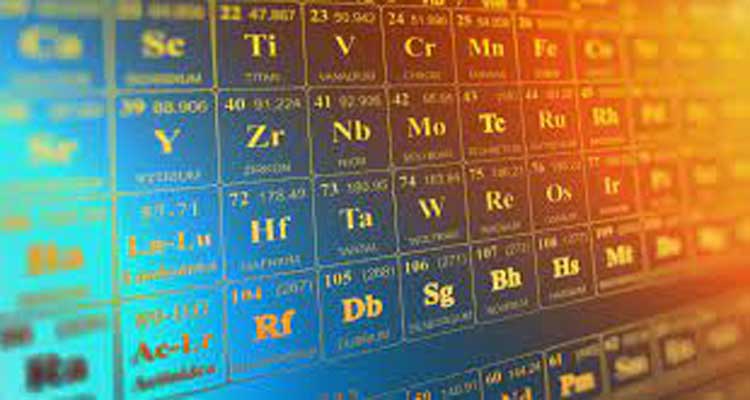
ArcelorMittal تولید میله سیم در Gijon را به دلیل رکود بازار به حالت تعلیق درآورد
یک شنبه, 14 شهریور 1400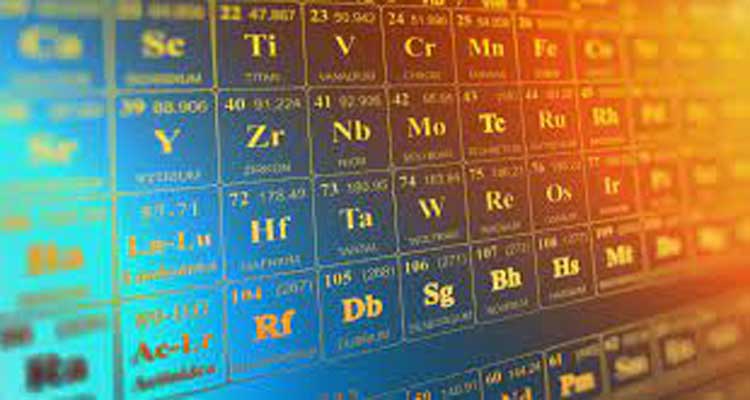
فیچ پیش بینی قیمت سنگ معدن را برای سال 2024 به 110 دلار در هر تن افزایش داد
یک شنبه, 14 شهریور 1400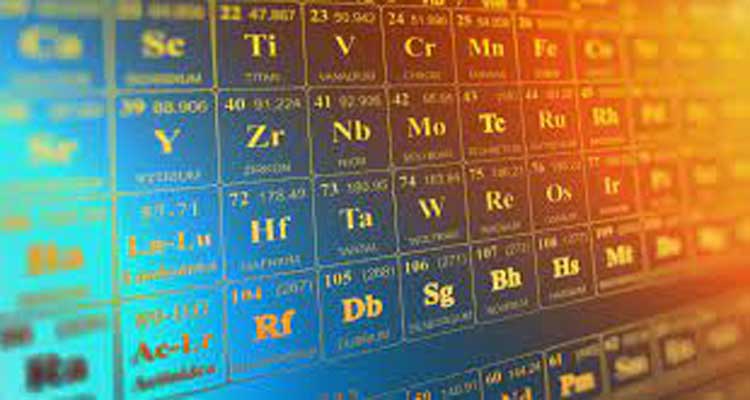
هند واردات سنگ معدن را در ماه نوامبر به بالاترین حد خود در 6 سال گذشته افزایش داد
یک شنبه, 14 شهریور 1400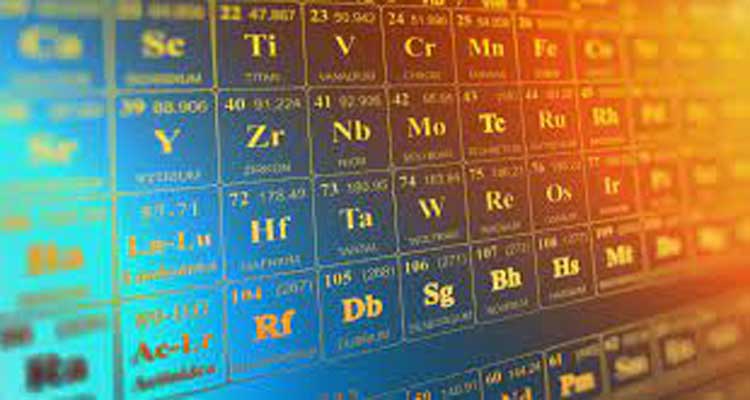
CBAM و سیستم سهمیه بندی مشکلاتی را برای صنعت فولاد اتحادیه اروپا ایجاد می کند
یک شنبه, 14 شهریور 1400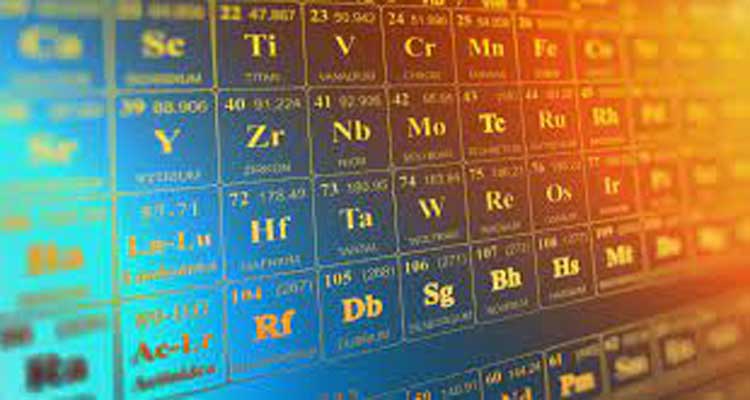
فروش فولاد در آلمان در ماه اکتبر 7.4 درصد نسبت به سال گذشته افزایش یافت
یک شنبه, 14 شهریور 1400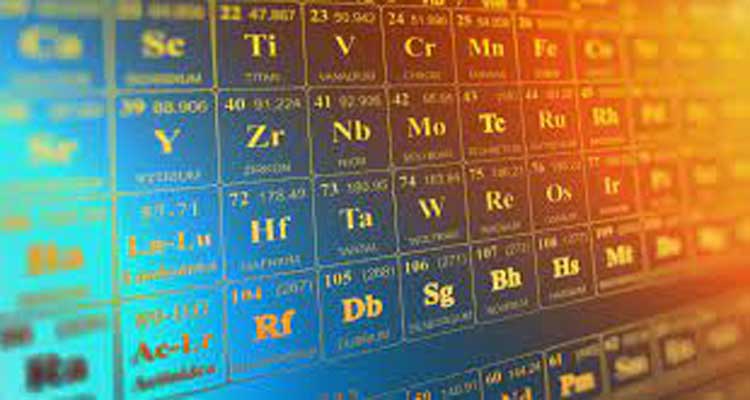
ترکیه صادرات میلگرد را در ماه اکتبر 28.3 درصد نسبت به سال گذشته کاهش داد
یک شنبه, 14 شهریور 1400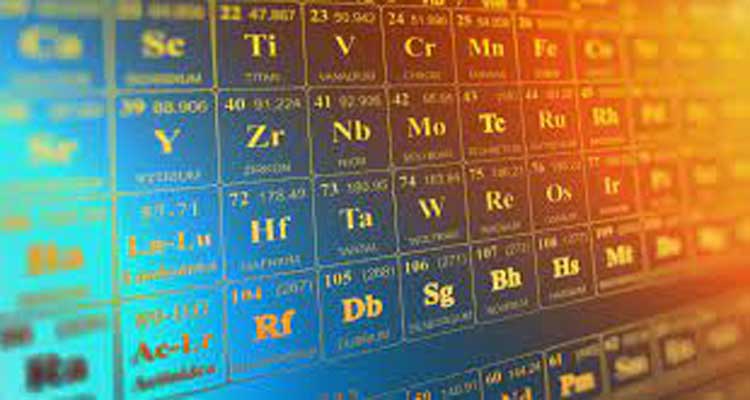
فولادسازان چینی در بحبوحه مشوق های اقتصادی در ماه های ژانویه تا اکتبر ضرر خود را کاهش دادند
یک شنبه, 14 شهریور 1400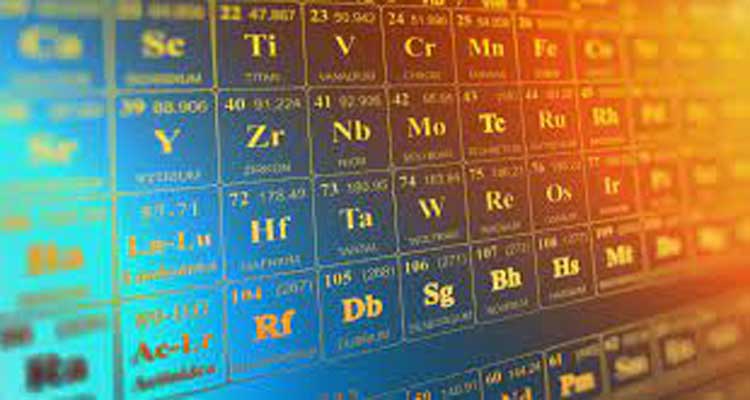
EUROFER بر یک برنامه کاربردی اروپایی برای صنعت فولاد اصرار دارد
یک شنبه, 14 شهریور 1400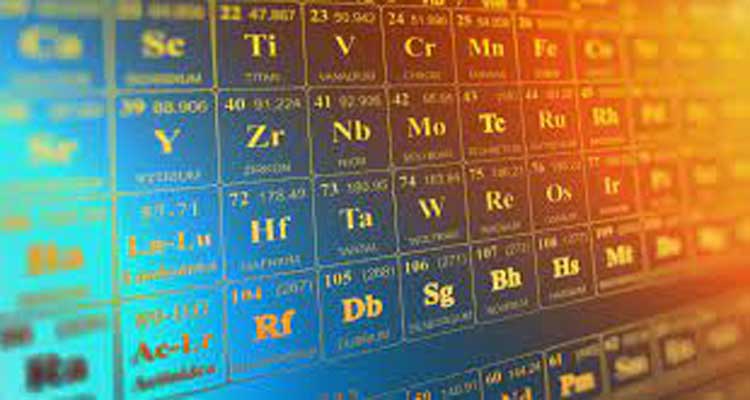
ترکیه در ژانویه تا سپتامبر بیش از 1 میلیون تن سنگ آهن از اوکراین وارد کرد
یک شنبه, 14 شهریور 1400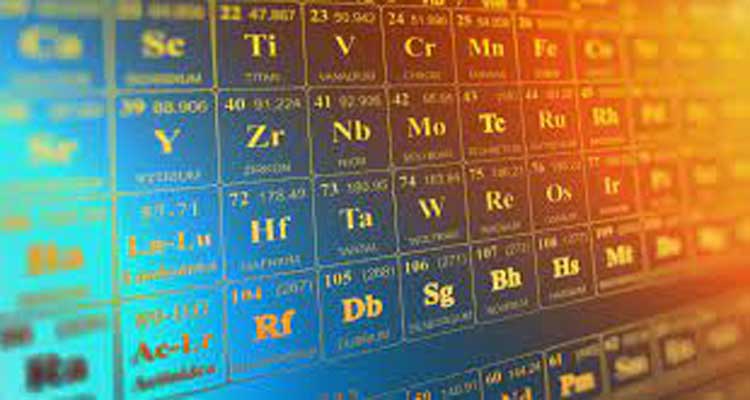
فولادسازان اروپایی خواستار محدودیت در صادرات قراضه شدند
یک شنبه, 14 شهریور 1400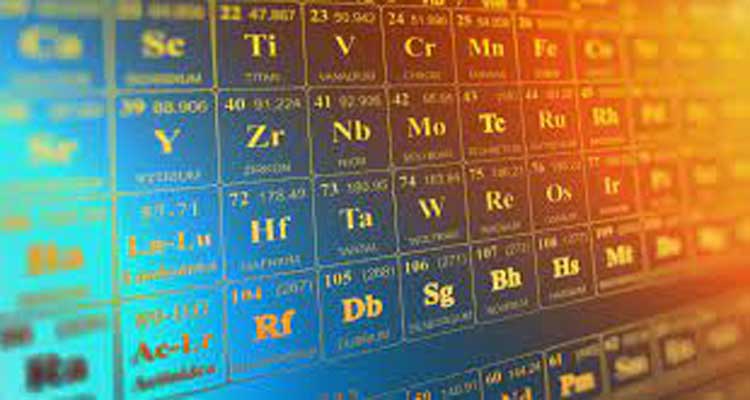
صنعت فولاد اروپا وعده اقدامات حمایتی بیشتری را داد
یک شنبه, 14 شهریور 1400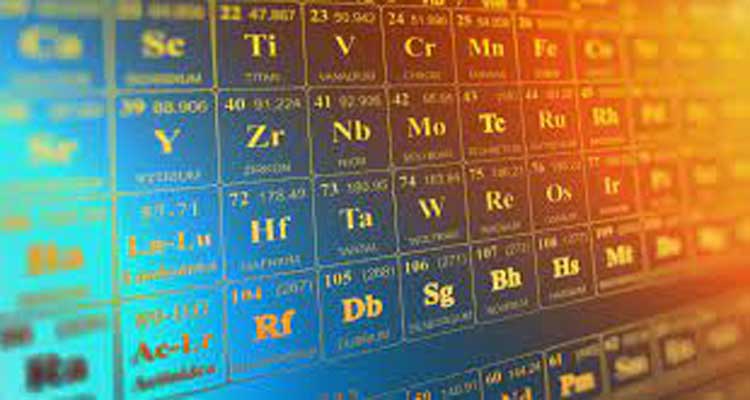
Nucor لوئیزیانا به رکورد جهانی تولید DRI در روز رسید
یک شنبه, 14 شهریور 1400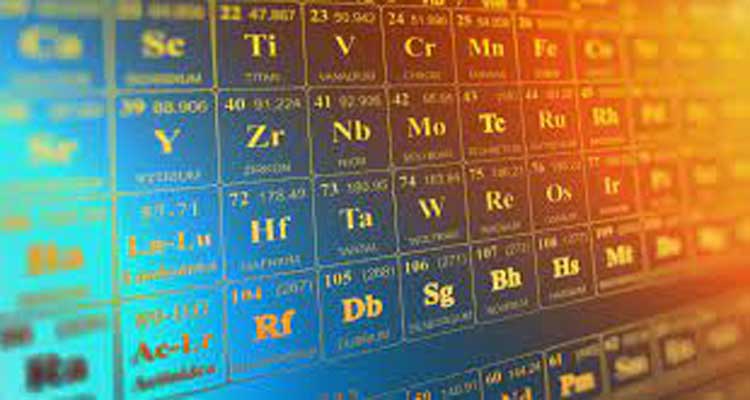
ارسال نظر